The world of metal casting has advanced leaps and bounds in the last few decades, with innovators introducing cutting-edge technologies such as 3D printing and sustainable practices. This article will discuss these new developments and how they are revolutionizing the art of producing cast metal products.
Well, explore the advantages that come from utilizing these modern techniques, as well as their potential limitations. From reducing production costs to improving environmental sustainability, there is no doubt that innovation has improved this once-laborious process dramatically.
In addition, will examine some of the newest advancements in metal casting technology that have opened up possibilities for even greater efficiency. Finally, we will look at what lies ahead for this ever-evolving field and its impact on our lives going forward.
The Benefits of 3D Printing in Metal Casting

3D printing has revolutionized the metal casting industry, offering numerous benefits compared to traditional methods. In addition to being faster and more efficient, 3D printing offers higher-resolution detail on parts and components that are typically difficult or expensive to achieve with conventional techniques.
The process is also capable of producing complex shapes not possible through other means, making it an ideal choice for applications requiring intricate designs. Furthermore, 3D-printed molds can be reused multiple times while still maintaining their integrity, resulting in cost savings over time.
Finally, 3D printing reduces material waste since it only uses the exact amount of metal needed for a particular part or component. All these advantages make 3D printing a great option for businesses looking to improve their production processes while keeping costs down and staying environmentally friendly.
Technological Advances in Metal Casting Processes
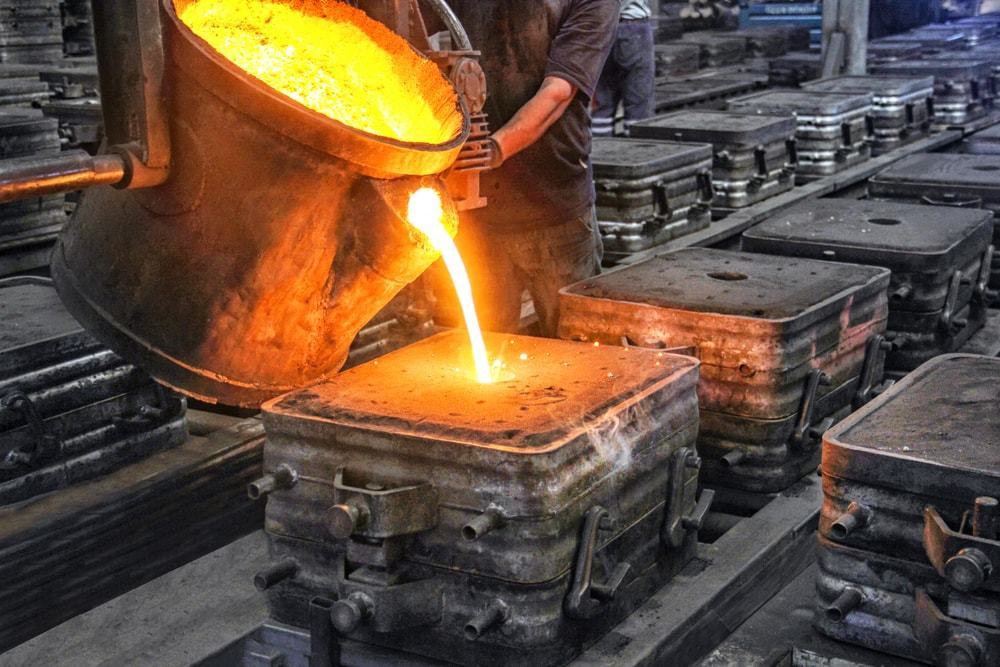
Recent technological advances have revolutionized the metal casting process. 3D printing has made it possible to create complex shapes and intricate details that would previously be impossible with traditional methods.
In addition, sustainable practices such as using recycled metals can reduce costs while helping protect the environment. This combination of advanced technology and environmentally conscious production makes metal casting a more viable option for many industries today than ever before.
Computer-aided design (CAD) software allows for precise part measurements, ensuring accurate designs are produced every time. Automation is also used to streamline the process by reducing manual labor and improving efficiency in plants and factories across the globe.
Advances in technologies such as robotic welding increase accuracy, speed up production times, and decrease waste materials while creating higher quality products at a lower cost than ever before. Thanks to these advancements in metal casting processes, manufacturers now have access to faster turnaround times without sacrificing quality or performance standards — enabling them to produce goods quicker with fewer resources consumed along the way.
The ability to print parts on demand makes it easy for companies to quickly generate molds when needed without having large stocks of inventory on hand – allowing them greater flexibility when responding to fluctuations in demand from customers.
Sustainable Practices for Metal Casting Operations

Metal casting operations are an integral part of many manufacturing processes, but their environmental impact can be significant. To reduce their negative effects and promote sustainability, innovative solutions have been developed to improve the efficiency of metal casting operations.
One such solution is 3D printing technology which enables fabricators to produce intricate components with greater accuracy and precision than traditional methods. This reduces energy use while also reducing scrap material waste.
Additionally, 3D printing eliminates the need for complex molds, saving time and money in production costs. Another sustainable practice that has been adopted by metal casters is the implementation of efficient cooling systems which help conserve water usage while ensuring that castings remain within specification tolerances during production.
The use of recycled materials in place of new resources can also create a more sustainable casting process as it helps lower resource consumption and minimize waste output from factories. Finally, replacing obsolete equipment with more energy-efficient models can considerably reduce emissions associated with metal casting operations while increasing productivity at the same time.
Innovative technologies and practices are helping to make metal casting operations more environmentally friendly by decreasing resource consumption and emissions generated during production processes while maintaining quality standards at the same time. With these advancements, manufacturers now have access to improved methods for producing high-quality components that meet customer demands without compromising on sustainability or safety requirements
Safety Considerations in Modern Metal Casting
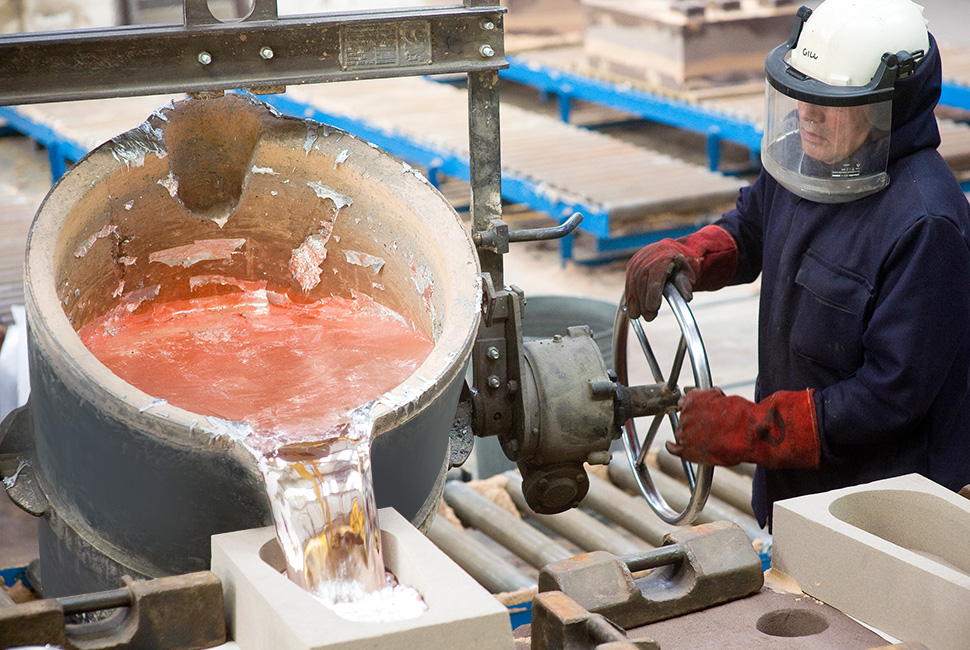
Modern metal casting has come a long way and has improved in many ways, from 3D printing to sustainable practices. However, safety considerations must never be overlooked.
Operators must ensure that all casting equipment is inspected regularly and kept in good working order; proper safeguards should be implemented for workers’ protection when operating the machinery. Additionally, the workplace should always have adequate ventilation due to fumes produced by melting metals as well as other hazardous materials used in the process.
Furthermore, any hot surfaces or liquids should also be properly labeled with warning signs and heat-resistant barriers to protect people from burns or scalds. Finally, employers should provide their employees with appropriate personal protective gear such as gloves and respirators if their duties require them to work closely with molten metals or harsh chemicals.
In conclusion, while modern metal casting may enable new production methods and reduce waste significantly there are still important safety measures that everyone involved must adhere to for a safe work environment.
Conclusion

Metal Casting has come a long way in recent years, with innovations ranging from 3D printing to sustainable practices. These advancements have allowed Metal Casting to become more efficient and cost-effective, while also allowing for the creation of products with greater precision and quality.
With this improved technology, metal casting can now create products that are more durable and last longer than before. As metal casting continues to evolve with new technologies, it is sure to remain an important part of modern manufacturing processes for many years to come.